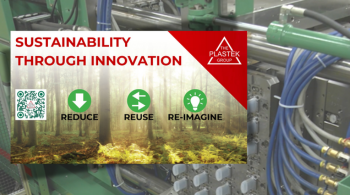
Sustainability is no longer just a buzzword—it’s a fundamental aspect of modern manufacturing. As industries across the globe strive to reduce their environmental impact, injection molding, a critical process in the production of plastic parts, is also undergoing significant changes. This blog post delves into the importance of sustainability in injection molding and explores how manufacturers can embrace greener practices.
The Environmental Impact of Traditional Injection Molding
Injection molding is widely used for producing plastic parts due to its efficiency and ability to create complex shapes with high precision. However, traditional injection molding processes can have a considerable environmental footprint. This is due to factors such as:
- High Energy Consumption: The process requires significant energy, especially in the melting of plastic materials and the operation of large machinery.
- Material Waste: While injection molding is generally efficient, some waste is inevitable, particularly during the initial setup and fine-tuning of the process.
- Use of Virgin Plastics: Traditionally, virgin plastics have been the primary raw material, contributing to the depletion of fossil resources and increasing plastic waste in the environment.
Key Strategies for Sustainable Injection Molding
To reduce the environmental impact of injection molding, manufacturers are adopting several strategies aimed at sustainability. Here are some of the most effective approaches:
Energy Efficiency
Energy consumption is one of the most significant contributors to the carbon footprint of injection molding. By implementing energy-efficient practices and technologies, manufacturers can reduce their environmental impact. Key steps include:
- Upgrading to Energy-Efficient Machinery: Modern injection molding machines are designed to be more energy-efficient, often featuring variable-speed drives and advanced heating systems that reduce energy consumption.
- Optimizing Process Parameters: Careful control and optimization of process parameters, such as temperature and cycle times, can lead to significant energy savings.
- Implementing Energy Management Systems (EMS): EMS allows manufacturers to monitor and optimize energy usage across the production process, identifying areas where consumption can be reduced.
Reducing Material Waste
Minimizing material waste is crucial for sustainable injection molding. Strategies include:
- Recycling and Reusing Plastic Materials: Many manufacturers are now using regrind, or recycled plastic, in their production processes. This not only reduces waste but also lessens the reliance on virgin plastics.
- Improving Mold Design: Advanced mold design techniques, such as conformal cooling and optimized runner systems, can reduce the amount of excess material required, leading to less waste.
- Implementing Lean Manufacturing Practices: By focusing on efficiency and reducing waste throughout the production process, manufacturers can minimize material loss and improve sustainability.
Sustainable Material Selection
Choosing sustainable materials is a crucial component of green injection molding. Options include:
- Biodegradable Plastics: These materials break down more easily in the environment, reducing long-term waste.
- Bio-based Plastics: Made from renewable resources like corn starch or sugarcane, bio-based plastics offer a more sustainable alternative to fossil-based plastics.
- Recycled Plastics: Incorporating post-consumer or post-industrial recycled plastics into the production process can significantly reduce the environmental impact.
Reducing Carbon Footprint
Manufacturers can take additional steps to reduce their overall carbon footprint by:
- Utilizing Renewable Energy Sources: Powering injection molding facilities with renewable energy, such as solar or wind, can drastically reduce carbon emissions.
- Optimizing Logistics: Streamlining the supply chain and reducing transportation distances can further cut down on carbon emissions.
- Engaging in Carbon Offset Programs: For unavoidable emissions, companies can participate in carbon offset programs to neutralize their impact.
The Role of Innovation in Sustainable Injection Molding
Innovation plays a key role in advancing sustainability in injection molding. Emerging technologies and practices are making it easier for manufacturers to adopt greener processes without sacrificing quality or efficiency.
Smart Manufacturing and Industry 4.0
Industry 4.0 technologies, such as IoT (Internet of Things) and AI (Artificial Intelligence), are revolutionizing injection molding. By enabling real-time monitoring and predictive maintenance, these technologies help reduce energy consumption and material waste. Additionally, smart manufacturing allows for more precise control over the production process, leading to greater efficiency and sustainability.
Advanced Recycling Techniques
New recycling technologies are making it possible to recycle a wider range of plastics and incorporate higher percentages of recycled material into products. These advancements are essential for creating a circular economy in the plastics industry.
3D Printing and Rapid Prototyping
While traditionally seen as a separate manufacturing process, 3D printing is increasingly being integrated with injection molding. It can be used for rapid prototyping, reducing the need for multiple iterations of molds and thus cutting down on material waste and energy use.
The Business Case for Sustainable Injection Molding
Adopting sustainable practices in injection molding is not only beneficial for the environment but also makes good business sense. The demand for eco-friendly products is rising, and consumers are increasingly making purchasing decisions based on a company’s environmental credentials.
- Regulatory Compliance: As governments worldwide introduce stricter environmental regulations, sustainable practices in injection molding can help manufacturers stay compliant and avoid potential fines or penalties.
- Cost Savings: While the initial investment in sustainable technologies and practices may be high, the long-term cost savings can be substantial. Reduced energy consumption, lower material waste, and improved process efficiency all contribute to lower operating costs over time.
It’s Time to Choose Sustainability
Sustainability in injection molding is not just an option—it’s a necessity for the future of manufacturing. By adopting energy-efficient practices, reducing material waste, selecting sustainable materials, and embracing innovation, manufacturers can significantly reduce their environmental impact while also reaping the benefits of cost savings, regulatory compliance, and enhanced brand reputation.
As the world moves towards a more sustainable future, the injection molding industry has a crucial role to play. By taking proactive steps now, manufacturers can ensure that they are part of the solution to the global environmental challenges we face.