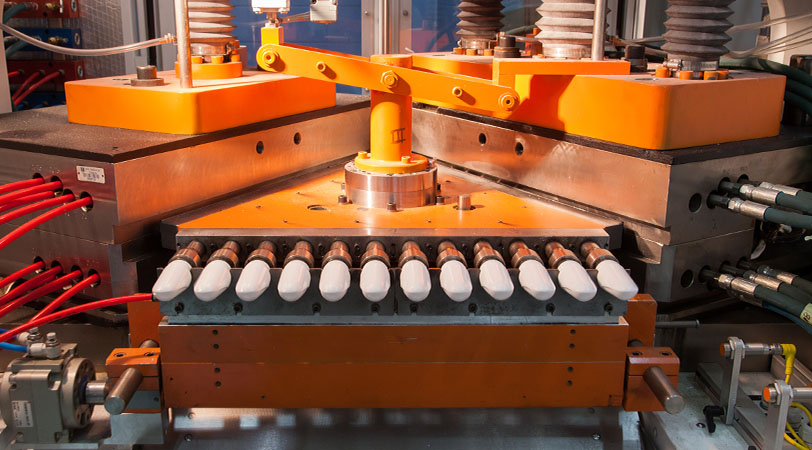
There are various methods of plastic molding, from injection molding for high accuracy to rotational molding for larger hollow products. By understanding how different plastic products are molded, you can select a molding process that satisfies the unique demands of your product or services.
Manufacturing companies offer different plastic molding options that are ideal for a range of industries, including personal care supplies, health and beauty products, home care items, pharmaceutical and nutraceutical products, and food and beverage items. This guide explores the different types of plastic molding processes and their common uses to help you determine the right molding manufacturing for your product or packaging.
What Is Plastic Molding?
Molding involves placing liquid or pliable material into a rigid frame or mold cavity to form a particular shape. The manufacturing process uses pressure and heat to fill the cavity and pressurize the material until it solidifies. In plastic molding, manufacturers use polymers like polypropylene or polyethylene in pellet, granule, liquid, or powder forms.
The result is various plastic products like vehicle parts, containers, bottles, bottle caps, syringes, and more. Plastic molding offers numerous advantages, such as faster production, enhanced strength, and accurate complex part design. As a result, plastic molding is the preferred molding method for numerous business types and their applications.
7 Common Types of Plastic Molding
Different types of plastic molding suit diverse industry needs, each with unique features and benefits. By understanding the different molding processes and their common uses, you’ll be better positioned to choose a type that provides optimal performance for your product.
Here are seven of the most common and effective plastic molding types you’ll want to consider.
1. Injection Molding
Injection molding is one of the most versatile and popular molding processes due to its capability to create parts with varying shapes and sizes. The injection molding process involves injecting molten plastic material into a metal mold at high pressure.
Injection molding is commonly used for everything from large plastic car parts to small plastic bottle caps. This type of molding is especially ideal for creating high volumes of precise and high-quality parts at an affordable cost.
For the best results, you must ensure the molding company you work with has high-performance molding machines and high cavitation single face and stack molds. This equipment allows for the most effective and accurate injection molding process.
2. Blow Molding
Blow molding is the process of making hollow, thin-walled plastic parts. This molding approach is often beneficial when the shape of your product is important and you need uniform wall thickness.
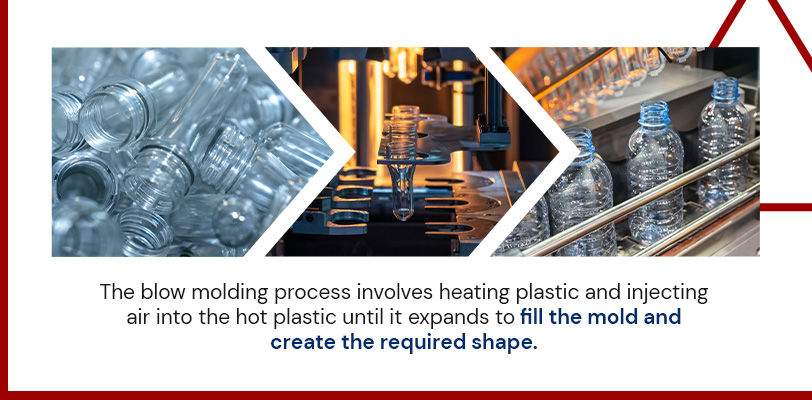
Similar to glass blowing, the blow molding process involves heating plastic and injecting air into the hot plastic until it expands to fill the mold and create the required shape. The mold then cools and hardens, and the machine ejects the part.
Some examples of products created through blow molding include plastic bottles, watering cans, storage containers, fuel tanks, and plastic drums. Blow molding is also a popular technique used in the pharmaceutical and nutraceutical industries and health and beauty industries — it can form containers, bottles, and small medical and single-serve vials. The process is fast, allowing you to produce many pieces in one day.
3. 3D Printing/Additive Manufacturing
The 3D printing process involves having a printer lay sequential layers of a material such as polylactic acid, nylon, or polycarbonate to create a product. At The Plastek Group, we can print three different colors and create components with features like over-molding or a soft-touch finish. One of the main benefits of 3D printing is that it allows engineers to design plastic parts from their desks and make them a reality in hours.
Given 3D printing’s flexibility, it’s a top choice for manufacturers in rapid prototyping, customization, and low-volume production scenarios. 3D printing also allows manufacturers to customize each item individually without incurring additional expenses, making it a cost-effective option for one-off or small-batch production needs.
4. Extrusion Molding
Extrusion molding forms long, cylindrical plastic objects. This plastic molding process also differs from other molding types in that it uses a die instead of a mold to shape the product. The process involves squeezing hot, raw plastic through a custom-shaped die to get the desired shape. The extrusion machine includes a screw that feeds the plastic resin to the feeder. As it passes through the die, it creates a long, consistent shape, which is often tubular.
Products formed with extrusion molding typically need to be the same shape along the length of the item. For this reason, companies mainly use it to create long and hollow products like straws, hoses, plastic decking, PVC piping, and plastic gutters. Some manufacturers may even create varying continuous shapes like U-sections, L-sections, T-sections, and circular sections.
5. Thermoforming
Thermoforming is a type of molding process that involves heating a plastic sheet of thermoplastic to a pliable forming temperature. A mold will then help the sheet form a particular shape, and a molding expert will trim it as necessary. This method also uses low pressures and can create 3D products from a 3D mold made from aluminum.
Depending on the product, the thermoplastic used in thermoforming will have varying thicknesses, materials, colors, and finishes. Professionals use thin-gauge thermoforming to manufacture containers, trays, lids, disposable cups, and similar products. Thick-gauge thermoforming is suitable for products like refrigerator liners and vehicle beds.
6. Compression Molding
Compression molding involves placing a heated plastic material into a heated mold and pressing it into a particular shape. This heating process, known as curing, allows the plastic to retain its strength. It is then followed by the cooling and trimming of the plastic before removal from the mold.
Compression molding is mainly useful for companies requiring strong, highly durable products. This process is ideal for automotive parts. Other valuable uses include creating sturdy plastic parts for household appliances, body armor, and clothing fasteners.
7. Rotational Molding
Rotational molding, or rotomolding, is ideal for producing larger hollow products or parts. The manufacturing process begins with placing liquid or powder resin into a metal mold and rotating it at high temperatures until the entire mold is coated with the resin. This constant rotation allows the resin to coat the mold evenly and create equal thickness throughout the product walls.
Rotomolding is one of the more economical molding options because you can reuse leftover plastic, reducing waste. You may use rotational molds for bulk containers, kayak hulls, recycling bins, storage tanks, and dog houses, among other products.
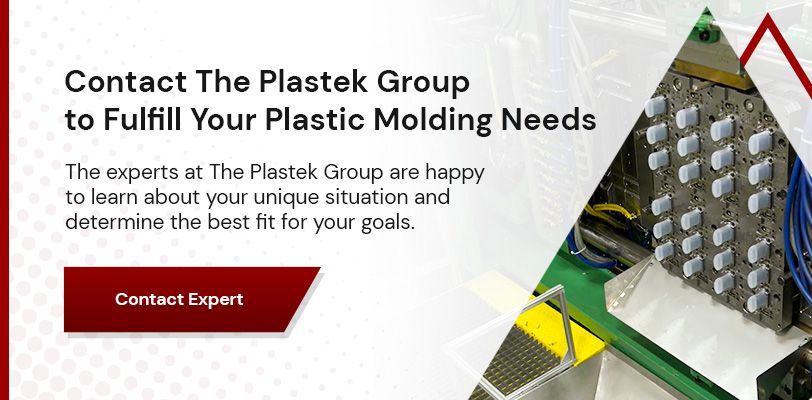
Contact The Plastek Group to Fulfill Your Plastic Molding Needs
Knowing the different types of plastic molding available can help you choose a method that aligns with your products’ needs. Would you like further assistance with understanding how to mold plastic and which molding process is best for you? The experts at The Plastek Group are happy to learn about your unique situation and determine the best fit for your goals.
The Plastek Group is a world-class manufacturing company for plastic injection and blow molding packaging, among many other value-added services. We have facilities in the United States, Mexico, Brazil and the United Kingdom so we can service leading companies across the globe. Our process involves understanding your project, analyzing the best way to meet your functionality and cost requirements, developing a manufacturable concept using cutting-edge software and other innovative tools, and creating the final working model.
Explore our plastic manufacturing capabilities today. To see how we can fulfill your plastic product and packing needs, contact one of our experts.