Original Author: Christina Fuges, Editorial Director, MoldMaking Technology
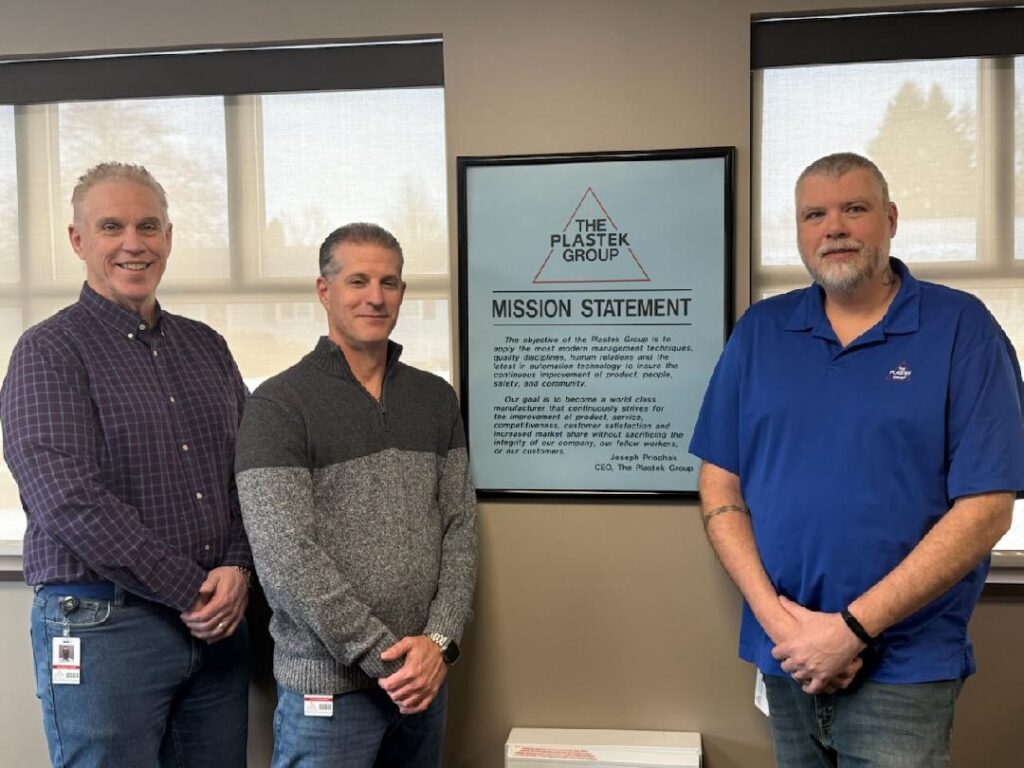
How would you describe The Plastek Group’s evolution in recent years?
Jason Bonanno, general manager, Triangle Tool, Tooling Division of The Plastek Group: It’s an evolution toward innovation and adaptability. The company’s core is stable, but we’re building on that foundation to embrace new technologies and methods. The family’s openness to change has been instrumental in this transformation.
Ray Luzier, director of Engineering, The Plastek Group: The Plastek Group has always been a pinnacle of molding excellence in northwest Pennsylvania. Joining this team has shown me how committed everyone is to maintaining that legacy while pushing boundaries. The culture here is forward-thinking, and I’m excited to be part of its future.
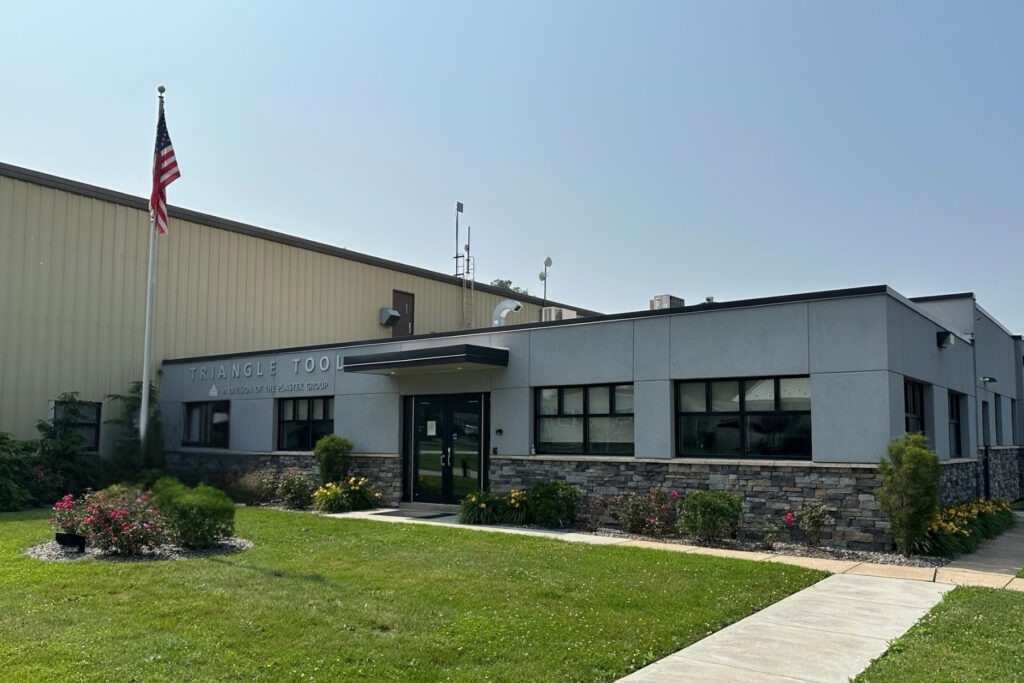
It has been five years since MMT covered Triangle Tool. This Tooling Division of The Plastek Group specializes in designing, building and manufacturing large-frame custom molds for high cavitation. Today, it is experiencing a quiet revolution, led by a few newcomers. Share your backgrounds and approaches to moldmaking.
Luzier: My career started in the late 1980s, working on highly precise electrical connector tooling. For over 20 years, I worked in various companies before briefly leaving the industry. F&S Tool later brought me back, where I gained experience that likely caught The Plastek Group’s attention.
I’ve noticed a strong adherence here to “We’ve always done it this way,” which provides stability but can also perpetuate past issues. Bonano, Corey Bratton (operations manager) and I are the newer hires hoping to introduce fresh perspectives to help modernize processes and improve efficiency.
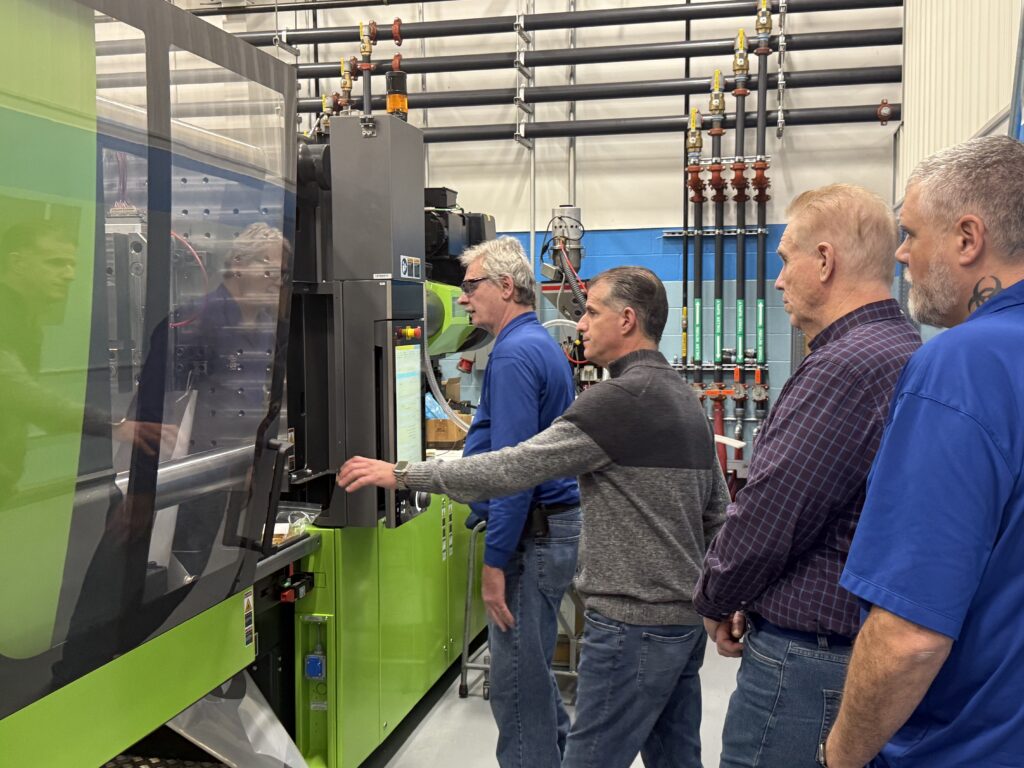
Bonanno: Collaboration is key. Having three leaders with varied perspectives has changed the culture within the tool shops. We’re moving away from comfort zones to embrace a transformative approach to manufacturing. For example, we’re focusing on digital tools, machine monitoring and efficiency improvements to optimize the entire process.
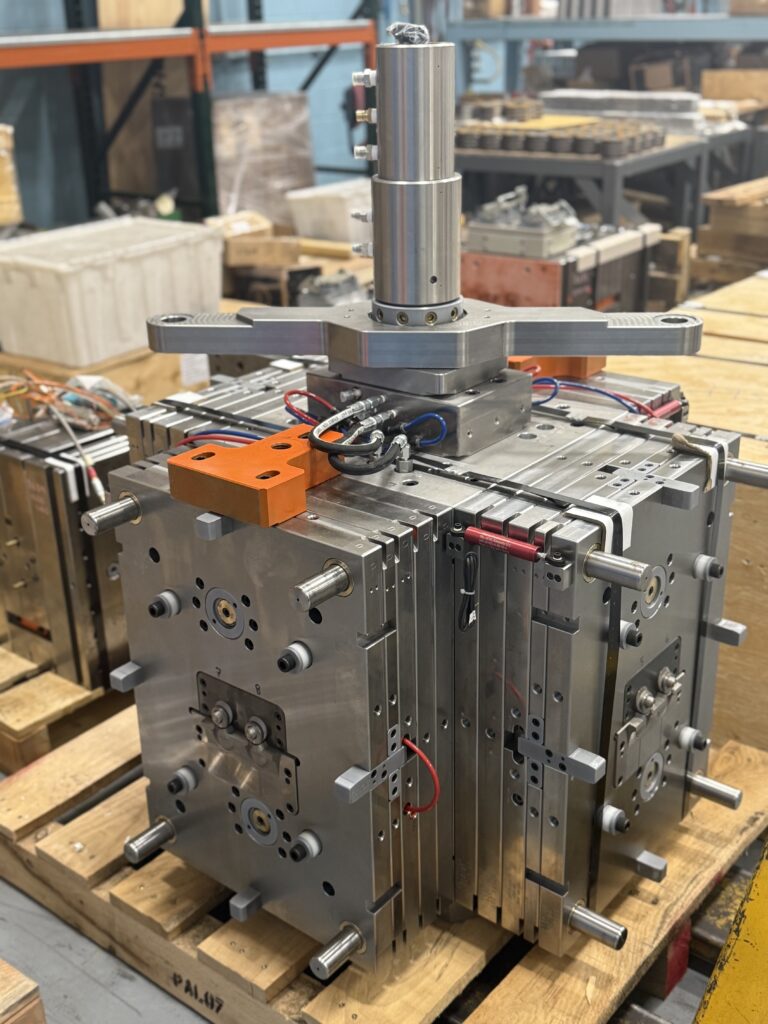
Can you give some examples of these cultural shifts?
Bonanno: A significant change has been implementing 3D design for all new projects. Surprisingly, some design work was still being done in 2D AutoCAD when we arrived. We’ve mandated 3D modeling to improve precision and efficiency, and we’re exploring going paperless. While this requires gradual implementation — such as introducing large monitors and digital tools — it’s about making changes that help the team work smarter, not harder.
Luzier: The shift to paperless operations has been challenging, especially for seasoned employees accustomed to physical drawings. However, we’re taking small steps, like making digital tools more accessible and demonstrating how these changes simplify workflows.
How are you addressing resistance to these changes?
Bonanno: It’s about tact and respect. I encourage team members to explain why they do things a certain way before suggesting alternatives. This approach fosters buy-in and uncovers long-standing pain points that we can address. It’s not about overturning processes but evolving them collaboratively.
Luzier: We’re also engaging seasoned employees to pass on their knowledge. It’s about motivating them to see the value of their legacy and the impact they can have on future generations.
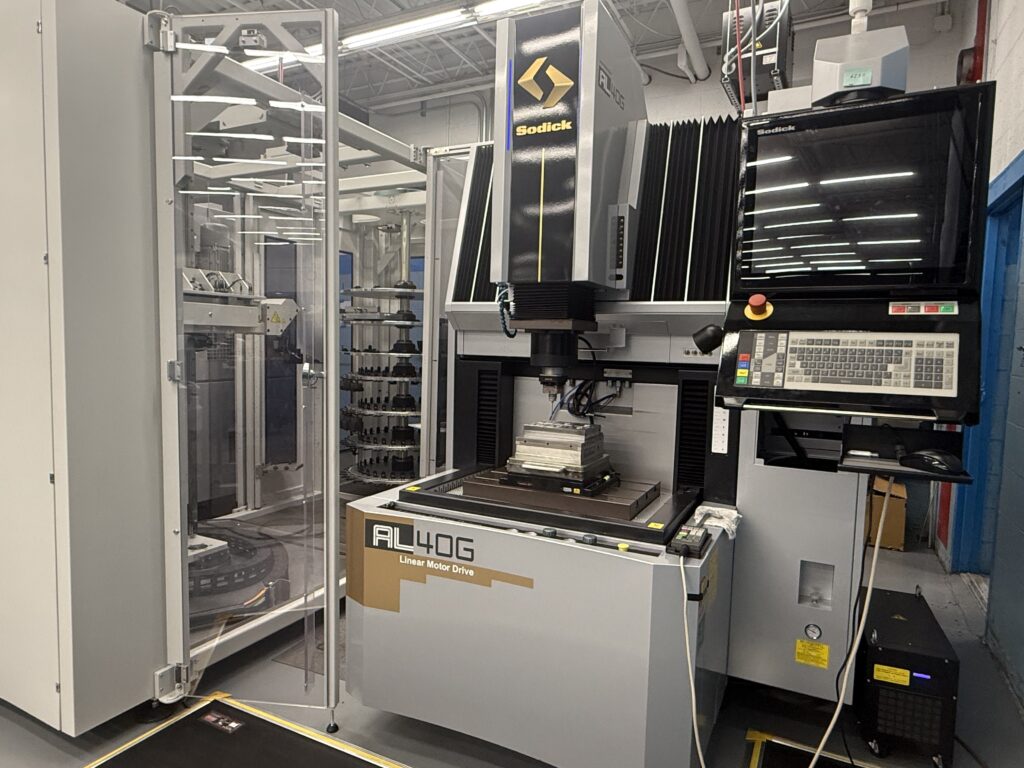
Let’s talk technology. What advancements and investments are being made?
Bonanno: We have a five-year capital expenditure plan with a $6 million annual budget focused on automation and new machinery. For example, we’ve invested in EDM machines that have already improved efficiency by 30%. We’re also introducing IoT monitoring systems for real-time insights into machine performance. This will enable us to target 95% operational efficiency, a standard for world-class operations. Automation is central to our strategy. We’re implementing systems like 3R robots for lights-out machining, where one operator can manage multiple machines. This streamlines operations and reduces downtime. We’re also considering adding a gundrill, which would eliminate the need for outsourcing and further integrate processes.
Luzier: On the 3D printing front, we’re experimenting with metal printing for mold components and using plastic printing for prototyping and fixtures. This reduces costs and lead times, providing more value to our customers.
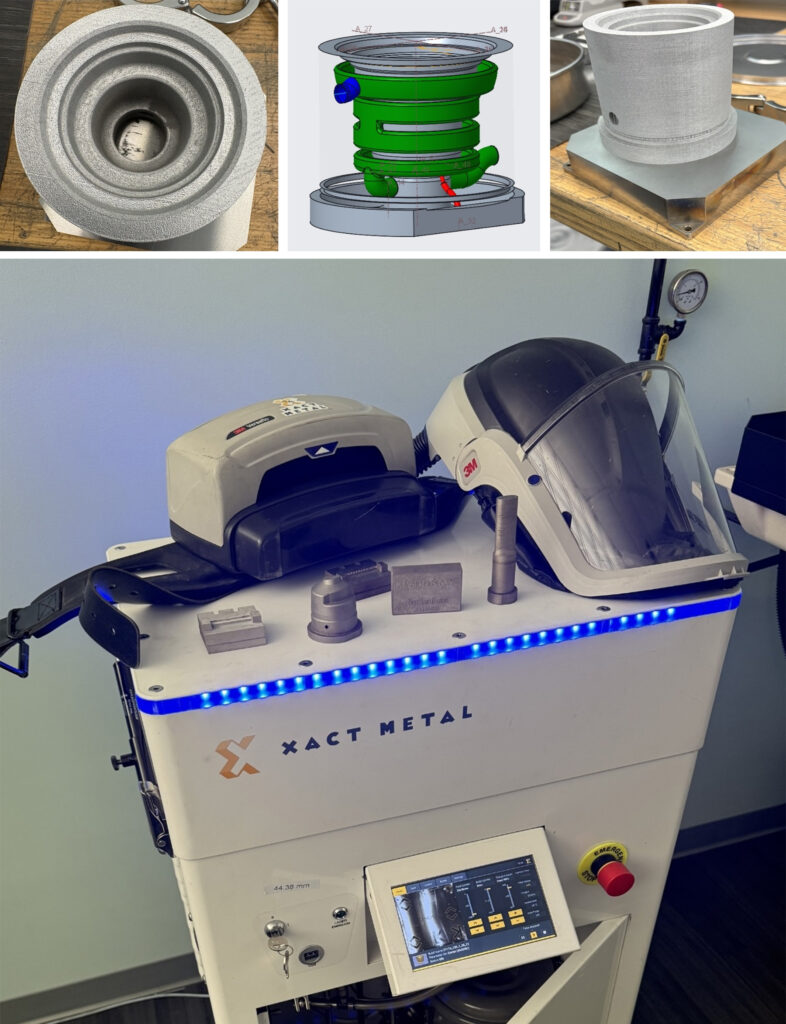
The Plastek Group has an international presence. How does collaboration with global teams shape operations?
Bonanno: The international collaboration is invaluable. For example, our UK team asked us to review tooling they inherited. Without prior knowledge of its challenges, Ray’s team identified 60% of the issues they were experiencing and he proposed solutions. This cross-learning strengthens our global operations and ensures consistency in quality.
Luzier: It also highlights cultural differences, such as safety standards, which vary by region. Sharing best practices benefits all locations and enhances overall efficiency.
Plastek Group continues to evolve, embracing innovation and adaptability while building on a stable foundation. With a strong commitment to molding excellence in northwest Pennsylvania, the company fosters a forward-thinking culture driven by leadership and a willingness to embrace change.
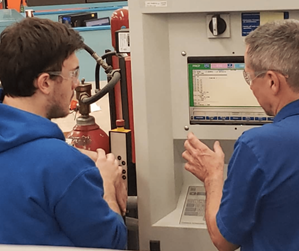
What challenges do you face in recruiting and retaining talent?
Bonanno: The shrinking talent pool is a major issue. We’re looking for a mix of seasoned professionals and younger talent comfortable with digital tools. However, motivating experienced workers to mentor younger employees can be challenging. By emphasizing their legacy and the importance of knowledge transfer, we’re fostering a more collaborative environment.
Luzier: Structurally, we’re moving away from the traditional “job leader” model to departmental leadership. This gives leaders ownership of specific areas like EDM, machining and assembly, which helps build stronger, more focused teams.
What specific educational programs or partnerships are you developing to ensure a continuous pipeline of skilled toolmakers?
Dennis Prischak, president and CEO of The Plastek Group: We uphold our internal apprenticeship programs and often recruit our students from job fairs as well as from current employees at Plastek who are seeking to advance their careers. It’s essential to promote the culture of precision on the toolroom floor and to showcase the latest technologies and software programming in order to attract young talent to the field. We believe that technology is a key factor in attracting talent, which is why we are committed to updating our fleet of EDMs, sinkers and five-axis mills.
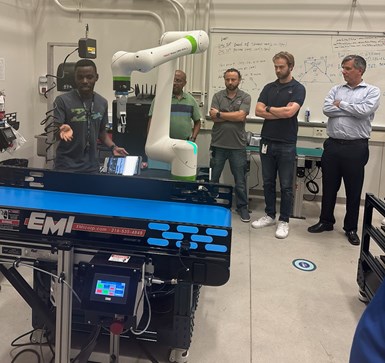
How does dedicating the Penn State Behrend Automation Lab to Joe Prischak reflect Plastek’s long-term commitment to workforce development?
Prischak: As the plastics industry and other manufacturing sectors continue to grow, automation will play an increasingly vital role in helping us stay competitive and relevant to our customers. The benefits of adding automation to manufacturing go beyond just boosting efficiency and productivity. Automation not only streamlines operations but also creates safer work environments, improves accuracy and quality, and helps businesses adapt to market changes. We’re experiencing this firsthand at The Plastek Group. So, the next logical and complementary step in education is to build on the four-year Plastic Engineering & Technology degree initiated by my father and others in the Erie area in 1989 with the Automation Lab.
Plastek and Penn State Behrend enjoy a rich history of collaboration as far back as Joe’s involvement in establishing the Plastics Programs at the School of Engineering. The robotics lab, dedicated in October 2023, is the latest commitment by the Prischak family to the department. The program focuses on technologies that help manufacturers compete globally, streamline efficiencies, and foster research and innovation among its students and industry. It gives students a hands-on approach to discovering the latest technologies and applying that knowledge to improving processing inefficiencies through the latest technical advancements and innovation in real-life situations.
The lab is equipped with robots, various sensor technologies and vision systems as well as manufacturing control systems. The facility was made possible through a $1.2 million gift from The Plastek Group, and specifically the family of its founder Joe Prischak. I also want to note that the Prischak family also offers an annual plastics scholarship to Penn State Behrend.
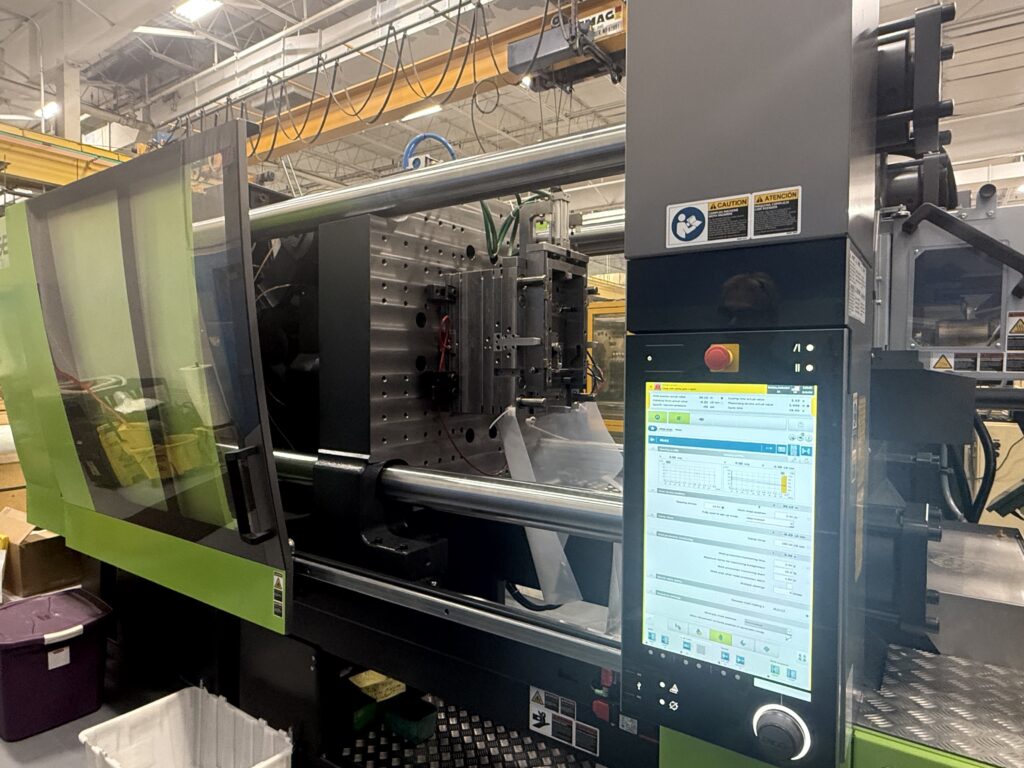
What about sustainability? How does it influence mold design and production?
Bonanno: Sustainability is a priority, especially as customers demand recyclable materials. This impacts material selection, coatings and mold designs. We’re working closely with hot runner suppliers to optimize for PCR (postconsumer resin) materials. While there’s still trial and error, the advances we’ve made are promising.
Luzier: From a moldmaking perspective, it’s mainly about ensuring durability and compatibility with various resins. Our molds are built to last, handling millions of cycles regardless of the material used.
Share an example of projects involving recycled materials, plant-based materials.
Prischak: The Plastek UK team won a Plastics Industry Materials Innovation Award at the annual Plastics Industry Dinner held in London in November. For this year’s entry, Plastek UK collaborated with Notpla, a supplier of seaweed-based polymers, to create a disposable fork made from seaweed for one of the rugby matches during the Six Nations Rugby Tournament in London in February. Plastek UK quickly built a one-cavity mold and using Notpla’s resin produced over 25,000 spoons for the event. Prince William attended the match and is pictured alongside the Plastek fork. This innovative fork was also showcased at NPE in May 2024.
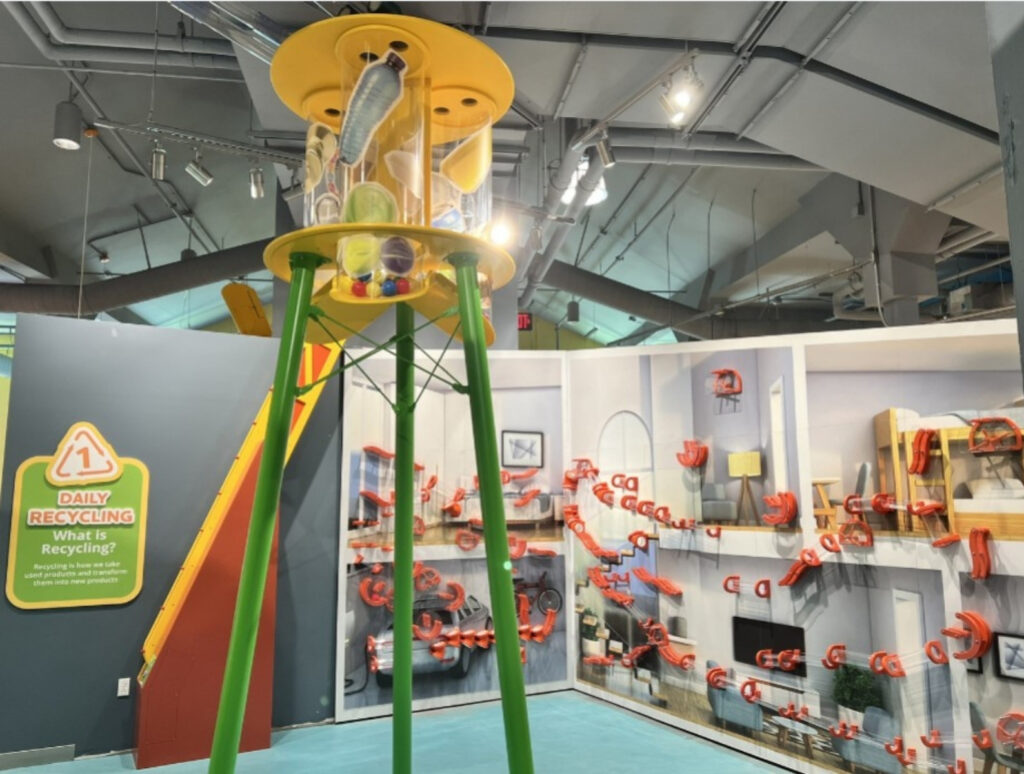
Tell me about the new recycling exhibit at the expERIEnce Children’s Museum in Erie and how it fits into your larger sustainability goals?
Prischak: Sustainability and reducing carbon footprints are the primary focuses for today’s manufacturers. Our customers increasingly ask us to explore lightweight products and repurposed materials. The objective of this exhibit is to introduce young people to the significance of committing to a circular economy for a truly sustainable future.
Plastic has often received a negative reputation in our country, and it is our responsibility in the industry to educate not only the current generation of young people but also their parents and family members about the benefits of responsible recycling methods. We must also inform them about how these recycled materials can be repurposed for various uses.
This exhibit serves as an educational tool to showcase a day in the life of a recycled plastic product. It begins with daily recycling tasks, such as separating materials, collecting, sorting, shredding, identifying and pelletizing.
Collaboration is key. Having three leaders with varied perspectives has changed the culture within the tool shops. We’re moving away from comfort zones to embrace a transformative approach to manufacturing.
What is the International Recycling Group in Erie (IRG)?
Prischak: IRG is dedicated to keeping plastic out of landfills by finding the most sustainable use for every grade of plastic and making sure nothing goes to waste. The plastic is collected and automatically sorted using near-infrared technology for maximized efficiency.
IRG was recently awarded a conditional loan from the U.S. Department of Energy to help finance construction of a new mechanical Supersized Plastic Recycling Facility (SuperPRF) plant, approximately 300,000 square feet, in Erie, Pennsylvania.
What phrase captures The Plastek Group’s trajectory?
Prischak: Endless possibilities. Forward-thinking innovation. Looking ahead, I see endless possibilities. We are exploring potential expansions into medical manufacturing while maintaining the strength of our core business. We remain committed to efficiency, sustainability and technological innovation, positioning the company as a forward-thinking leader in the moldmaking industry.